What I learned about the orchestration of processes, security and communication to shred hard drives securely and smoothly
At Guardian Data Destruction, data destruction is our first and most requested service, forming the cornerstone of our service operation. We excel in shredding hard drives and solid state drives, reducing them to dust particles as fine as 2mm. With the largest fleet of shred trucks spread across the country, Guardian delivers secure, onsite shredding services anywhere.
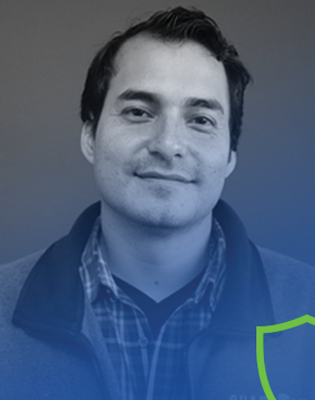
Recently, I had the opportunity to be a part of a shred job which provided first-hand insight into our process. As part of the Guardian marketing department, I’ve spent over a year engaging with and documenting our Shred Team drivers, technicians and operational staff. However, actively participating as a project unfolded and wrapped up was an eye-opening experience.
Pre-trip shred truck inspection
Guardian Road Warriors must ensure that everything is set to successfully complete a secure data destruction job. That responsibility includes a working vehicle, the right supplies and adherence to a time-tested shred process. Before embarking on a shred job, the driver carefully scans their assigned Guardian shred truck and reviews over 46 unique safety and readiness inspection points.
Chris Batres, our longtime Fleet Manager, ensures that each truck is fully operational and equipped for its scheduled job. The company uses Samsara, a safety, efficiency and sustainability monitoring app for electronic logs to ensure seamless truck operations and data tracking. As a result, Chris is in touch with the entire fleet’s movements, diagnostics and drivers wherever they are.
Once the inspection is complete, each assigned shred team loads the project equipment into the truck based on the specific SOW for each job. For my shred day, the truck was loaded with secure transfer bins and an empty Gaylord to catch the hard drive shred as it finished processing.
RELATED: Understanding safety ratings for logistics >
Project management
Before the trucks are prepped for scheduled projects, I learned that Guardian project managers are getting prepared. In addition to confirming arrival dates and times, they also confirm the size of the job, the quantity of what will be shredded (HDDs, SSDs, tapes, other), any security clearances required onsite, who our point of contact will be with numbers and emails, who the ITAD’s POC is and how to reach them for questions, outlined special circumstances or requests and anything else we’ll need to know like odd loading dock sizes, street parking requirements (especially for urban locations without loading docks) and added services like weight, video monitoring, auditing, scanning, verifications, etc. For this very small project, Dave Wasserman, the project manager, provided us with a complete, confirmed description of what to bring, where to go, who to ask for and what we were shredding. To me, it was simply a 45-minute drive to a secure data center where we were assigned to shred 45 high-capacity, sensitive hard drives.
Safe, CDL drivers are essential
Guardian’s shred trucks are operated by skilled drivers possessing a Class B Commercial Driver’s License (CDL). While Roberto Chaves, a true “Guardian of Data” Road Warrior, and experienced CDL project lead, wove through New Jersey traffic and highways, I enjoyed the elevated road perspective
As we drove, Roberto described what I’d be doing, security protocols and processes. He also noted that maintaining a steady conversation amongst the project team is a nicety but it’s also a critical safety measure that prevents drowsiness and potential accidents. Because Guardian’s 100+ technicians are on the road at many large-scale data destruction projects, shred jobs are often scheduled far away for successive days (sometimes weeks) and extend into long workdays to meet client deadlines. I understood that crew safety getting to and from every project is as important as data safety on the job.
Onsite project processes
Upon arrival at the onsite shred location, we contacted the designated Point of Contact (POC) and were admitted by the facility’s security gate attendant. Once the shred truck was parked at the loading dock, I got right to work following Roberto’s instructions.
The empty Gaylord was moved into place below the shredders and we unloaded the 32-inch bin from the “box” (which I learned was the cargo area of the truck). From the loading dock, we buzzed into a small dock room where we waited for the POC under the watchful eyes of two security guards in a glass-separated room.
Four of the client’s IT technicians joined us in the room. With them came a bin of end-of-life (EOL) HDDs and SSDs.
SSDs? Instantly the project had changed dramatically in asset type and quantity! (I learned that this happens on almost every job and that there’s a Guardian escalation and resolution process in place). Roberto immediately notified our project lead, Dave, who reached out to the ITAD who authorized us to shred the updated project scope: 153 HDDs to 20mm and 25 SSDs to 10mm shred. I don’t think there was even a five-minute delay while the decision-makers conferred and agreed!
RELATED: What happens when the project scope changes (on arrival) >
Using the new project quantities, Roberto and I, along with the client IT techs, meticulously counted and confirmed the updated HDDs and SSD numbers. As we counted, Roberto moved the drives individually to the Guardian secure transfer bin. Quantities now confirmed and accounted for, the bin was securely locked and we rolled it to the loading dock for shredding. Finally, some action!
Before the shredders or generator was turned on, Roberto showed me how to put on the required EHS (Environmental Health and Safety) PPE (Personal Protective Equipment) that is required to operate the equipment for their protection.
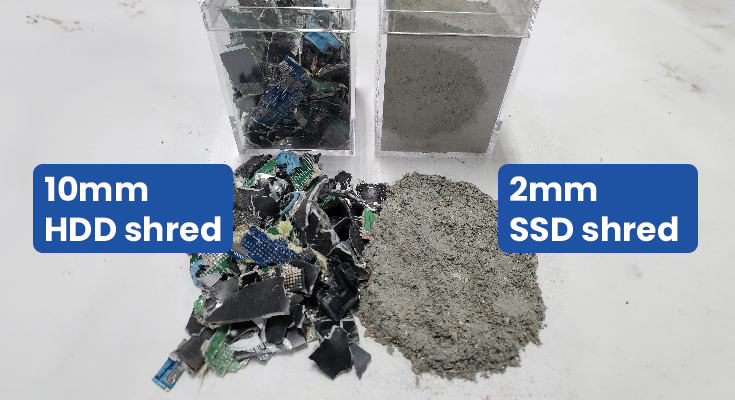
Onsite hard drive shredding
Each hard drive was pulled from the bin and placed onto the moving conveyor belt. I watched as the drives were fed and dropped into a bin equipped with sharp, spinning blades that loudly ripped and ground each drive into 20mm pieces that were dropped into the waiting Gaylord below.
The SSDs followed the same process using a separate shredder that ground them into small, 10mm particles that dropped into the same Gaylord. The entire 90-minute shredding process was observed by the four client IT techs who were safely positioned outside the truck box on the loading dock.
Chain of custody process
Documenting the chain of custody is an essential component of tracking the data sanitization process. I watched as Roberto completed and signed the Media Destruction Form (MDF) that listed exactly what we had received and then shredded. One of the customer IT techs confirmed the asset count and destruction again and then co-signed the MDF. The POC confirmed that the shred job was complete.
COMPLIANCE | Learn more about the importance of NIST 800-88 documentation
Shred job completion process
Once all the drives were shredded, the shredders and generator were powered off and I helped Roberto work his way through a post-shred job checklist to ensure a complete and secure project.
- The shredders were Inspected to ensure that drives/SSDs were not stuck on a side wall or in between cutters.
- The surrounding area of the truck box interior was inspected for any drives that may have fallen.
- The shred bin was inspected to confirm that everything was completely shredded.
- All tools and supplies were put away.
- All truck contents, including the Gaylord of shred, was secured for road travel.
Before we left the loading dock, Roberto sent the completed MDF to the Guardian project team and informed our dispatcher that the shred job was complete and we were heading back to Guardian headquarters “base”.
The journey back mirrored the ride to our destination. I had a lot of questions that Roberto answered and we also exchanged stories about our personal lives, work and interests. The entire shredding project, including the ride, shed some real insight into his experiences and just how important it was to be consistent and process-driven as a shred technician. I had participated to understand the Guardian data shredding process firsthand but the full experience was more secure, interesting and enriching than I had expected.
R2 recycling and the post-project inspection
The job wasn’t over yet! Once we returned to base, the warehouse manager, Bruce Kappes, greeted us with a forklift that removed the Gaylord from the truck. Now under his control and fully tracked for chain of custody, the shredded SSD and HDD pieces would be sealed, labeled and delivered to a local R2 recycler.
Roberto turned over project documentation and had a quick recap with Dave about the job and then we tackled the not-so-glamorous but important cleanup of the shred truck to prep it for the next day. The truck was swept clean and an inventory of needed supplies was sent to the Fleet Manager with notes about the truck, the generator and the shredders’ performance.
Finally, the Samsara app was clicked “off” and Roberto and I clocked out. He had another day on the shred truck in the morning for a different Channel Partner and their specific project details. I would be back to shred marketing but with a whole new perspective.
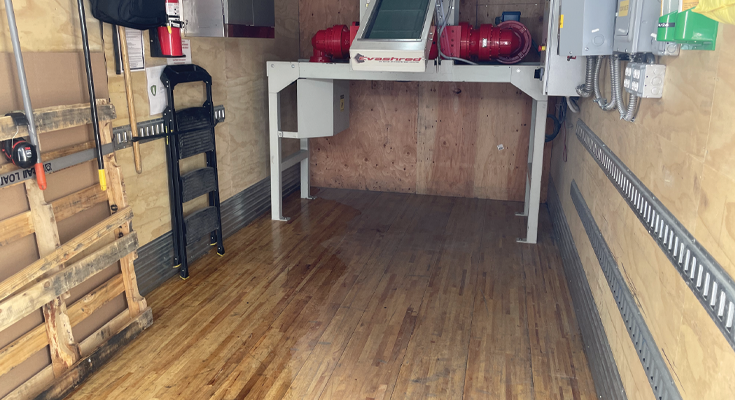
A Shred Technician-for-a-day’s takeaways
My onsite HD shred job experience was fleeting (less than three and a half hours including travel) but impactful. I was unprepared for how impressed I was by:
- The unflinching security that the client placed on checking our credentials, data destruction process, chain of custody and documents. We were never unsupervised with no less than seven people checking us in or witnessing the process.
- The rigor and pride that Roberto applied to his job. He followed Guardian processes throughout whether it was chain of custody, count verifications, health and safety protocols (including while driving and chatting with me), shredding the drives and even cleaning up.
- The constant flow of positive and functional communication between Guardian project managers, our channel partners, their customers (our onsite location) and the onsite team. The proven, established process covered project logistics, personnel expectations, scope changes, timings, paperwork and chain of custody. It completely kept everyone informed, to the minute, so that a surprise like a change in scope was a hiccup, not a headache.
- Data compliance and security are built into the Guardian code. From every touchpoint including warehouse staff, drivers, operations and shred technicians, no shortcuts were considered.
- The realization that the project would be reviewed, verified, invoiced and include a Certificate of Destruction for the exact number of drives that had been shredded – all within 72 hours of job completion!
My job is to create online content that represents Guardian. Being onsite, on an actual project, working alongside Roberto with assistance from Chris, Bruce, Dave and everyone else, I saw how Guardian’s Core Values and Customer Commitment are the foundation of Secure, Compliant and Absolute Data Destruction.
I was indeed a Guardian of Data – for a day.
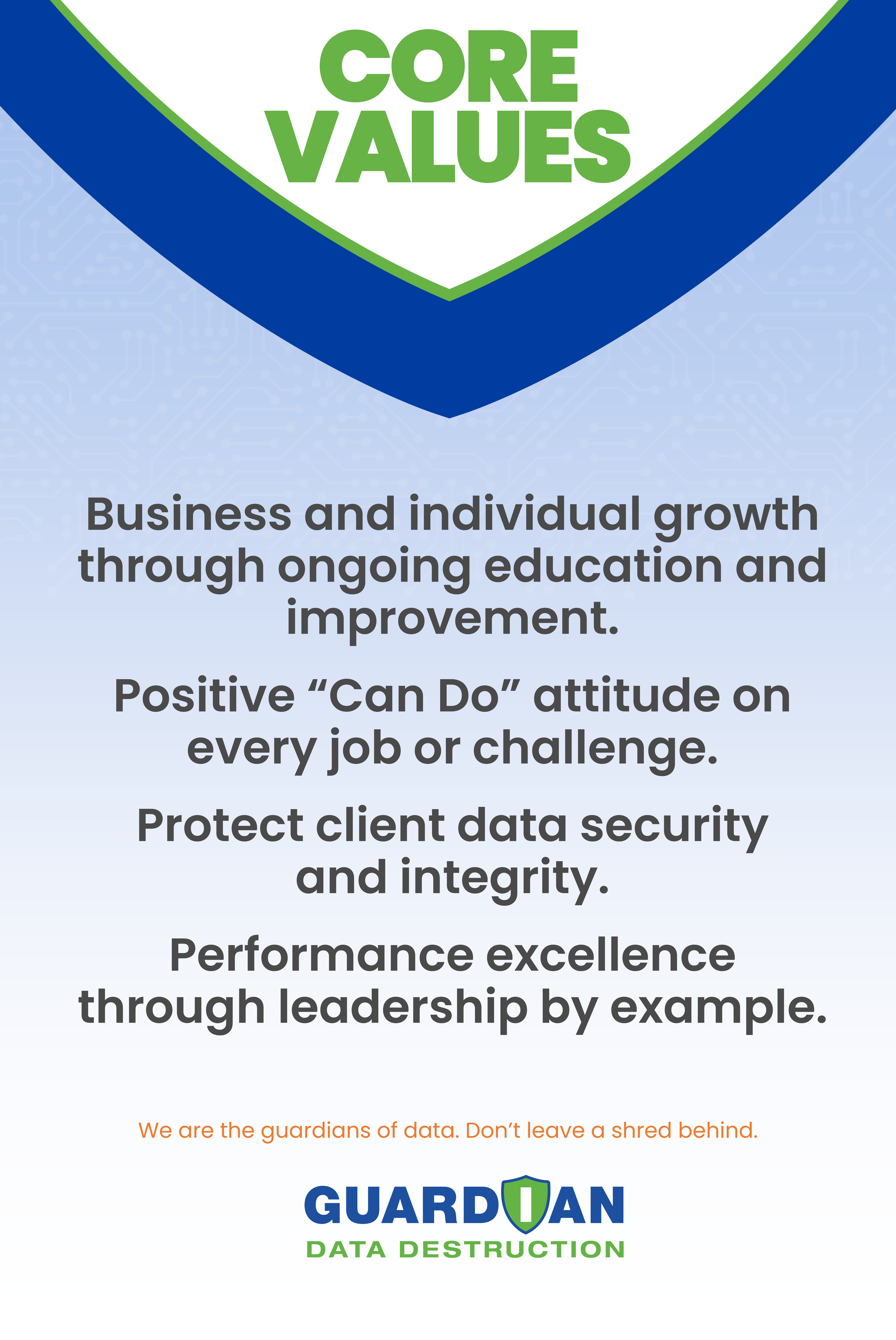
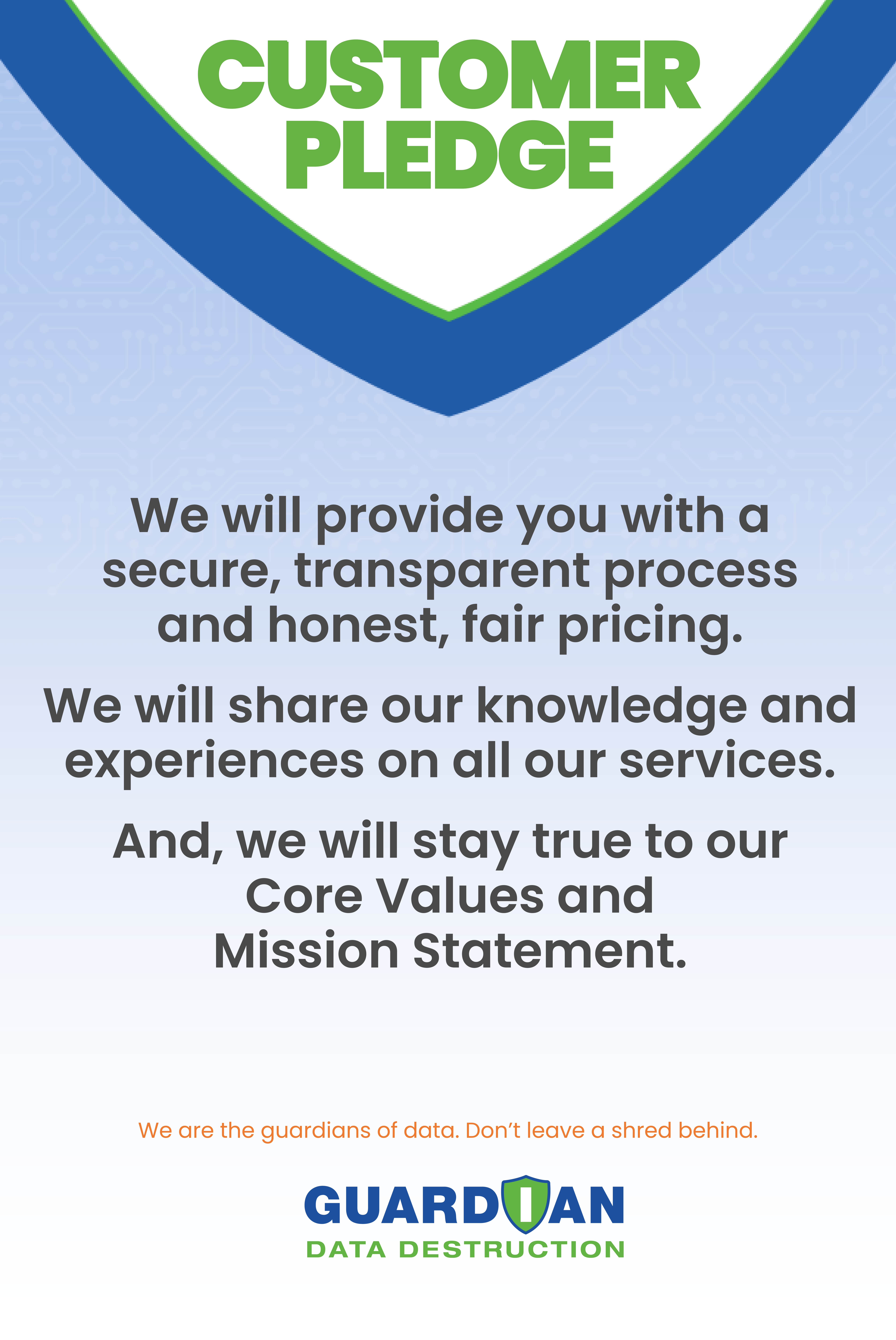
Read Next
- FAQs about hard drive shredding >
- How to scope a data destruction project to get the results you want >
- Guardian’s HDD, SSD and tapes shredding services >
- How data walks out facilities on unknown, undocumented data storage >
Sign up for email updates to receive the latest in data security options from Guardian Data Destruction >